Unfortunately, plastic waste is mostly a mixture of several different polymers. In the process of recycling plastics, Heterogeneous plastic mixture components are not compatible with each other. This incompatibility depends on the chemical structure of the mixed polymers. For example, PET and PP form separate phases in the production process of plastic products because they are chemically different from each other. Defects in the interface of polymers cause it to tear. Polymers that have different structures do not thermodynamically mix with each other and therefore a homogeneous mixture is not obtained. In the mixture, the polymer with a high concentration is considered as the continuous phase, and the polymer with a lower concentration is dispersed in the matrix or the continuous phase. However, the intermolecular adhesion between the continuous phase and the dispersed phase is very low, and it causes that desirable mechanical properties of this mixture are not observed. In order to create a homogeneous mixture of recycled polymer and thus improve the mechanical properties of polymer mixtures, compatibilizers are used. Compatibilizers modify the interface of polymers and prevent delamination by reducing the surface tension in the melt, preventing the growth of the dispersed phase, increasing adhesion at the interface between two phases, and minimizing phase separation in the solid state [1]. In the figure below is a schematic of the role of compatibilizer in recycled mixtures.

Figure 1. The role of the compatibilizer a) the performance of the compatibilizer b) the effect of the compatibilizer in processing the mixture [1].
The most suitable compatibilizer for each polymer mixture is selected based on the chemical structure of the polymer used, and in fact there is no general instruction for all mixtures. Therefore, any compatibilizer must be adapted based on the polymers present in the compound.
To create compatibility, reactive and non-reactive compatibilizers are used. Reactive compatibilizers form a covalent bond with polymer functional groups. The most common of these compatibilizers are maleic anhydride or acrylic acid grafted polyolefins or glycidyl methacrylate copolymers. Furthermore, reactive monomers can form compatibilizers in situ. Non-reactive compatibilizers are usually miscible with one of the blend components. Among these types of compatibilizers, ethylene-acrylic ester copolymers or styrene-butadiene-styrene block copolymers or styrene-isoprene block copolymers can be mentioned. The following examples show the effect of the presence of compatibilizers in heterogeneous recycled mixtures:
PE/PS mixture: This system was compatibilized with styrene–ethylene–butylene–styrene block copolymer (SEBS) in the range of 7% for blend compositions of 20/80 to 80/20. In the best case the Charpy impact strength increased by a factor of 4. Morphological characteristics showed a decrease of the size of the dispersed particles and an improved interfacial adhesion between both phases.
PE/PP mixture: PP impurities in PE cause the impact strength and elongation to decrease drastically. The addition of 2 to 10% of random copolymer of ethylene propylene (EP) showed that the impact strength will increase to an effective amount [1].

Additives and other processes to increase recycling quality
Coupling agents: Coupling agents are reactive molecules that react chemically with filler/fiber and polymer matrix, which increases the adhesion of the mixture components. Some reactive compatibilizers may act in the same way. Figure 2 shows the role of coupling agents in rubber composite. In general, coupling agents are low molecular weight reactive molecules, and are mainly used to increase the adhesion of rubber filler and glass fiber polymer adhesion; While compatibilizers are made of polymers and act mainly in polymer blends. Coupling agents are a wide range of chemical compounds, including fatty acids and their salts, such as calcium stearate, organic silanes that are widely used for glass fibers, titanates, zirconates, and anhydrides. For example, silane coupling agents increase the tensile strength, elongation and impact resistance of PP/PET blends. Titanate coupling agents could improve the elongation at break and slightly impact strength of mixed plastics at a concentration of 1% similar to chlorinated polyethylene where 10–20% were used [1].
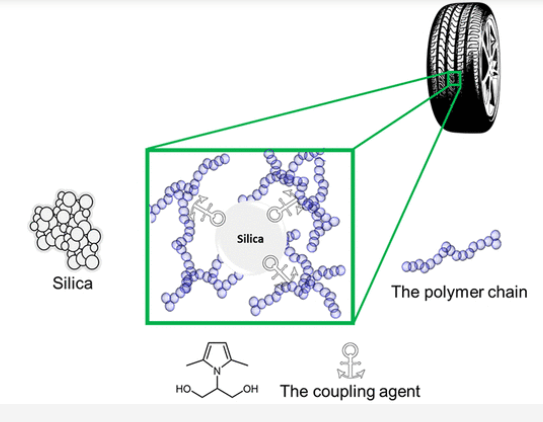
Impact modifiers: these modifiers are mainly butadiene-based elastomer compounds, such as styrene-butadiene-styrene (SBS), styrene-isoprene-styrene (SIS) or ethylene-propylene-diene copolymers (EPM and EPDM), which are often related structurally to the compatibilizers. By adding these modifiers to recycled materials, impact resistance and elongation increase, while modulus decreases. The appropriate choice of impact modifier depends on the specific plastic to be toughened; main applications are in PS, PP and engineering plastics such as PA, polybutylene terephthalate (PBT), PET [1].
Metal deactivators: Metal deactivators form complexes with metal ions and reduce the negative effects that metal has on the polymer, such as reduced oxidation stability. It has been observed in LLDPE nanocomposite that by adding UV absorbers benzotriazole, benzophenone and hydroxyphenyl triazine, the lifespan of the nanocomposite film has been improved. However, a metal deactivator (MD-1) alone outperformed the UV absorber in this test, indicating that the effect of metal impurities is very important [1].
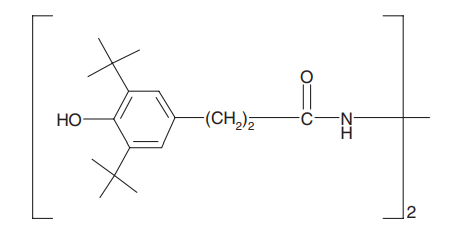
Melt flow adjustment: There are limited possibilities to adjust the polymer melt flow, according to the required transformation process. To increase melt flow (lower melt viscosity, lower molecular weight), for example, in polypropylene from radical generators such as peroxides, hydroxylamine esters or azoalkanes or in the field of polycondensation polymers (PET, PA) by hydrolytic cleavage is used. Processing aids, lubricants, waxes and addition of oligomers may help to improve processing, to lower the melt viscosity and to increase the throughput. To reduce melt flow (higher melt viscosity, higher molecular weight), in some cases, “repairing” molecules can be used, for example in polyamides, a combination of an active additive such as dioxiranes and an additive that has a catalytic effect [1].
Odor reducers: post-consumer recyclates suffer often from odor problems caused by contaminations or degradation products from the first application. Removing odor is a challenging task as very low quantities of volatile products can be the reason which are difficult to analyze or to trace back. Technically, odor can be reduced by adjusted processing including vacuum venting or vacuum venting in the presence of a carrier such as water. Another potential way to reduce odor is through additives, e.g., RS-3, zeolites or selected silicates [1].
Optical stabilizers: light, especially in the UV range, can cause the phenomenon of photooxidation, which causes the destruction and breakage of polymer chains. To prevent this phenomenon, light stabilizers are used. UV absorbers are among the oldest light stabilizers that absorb harmful UV rays and convert them into heat energy. In this way, UV absorbers protect vulnerable polymer chains. Benzophenone and benzotriazole are among UV absorbers. It should be mentioned that hydroxy benzophenone and hydroxyphenyl benzotriazole are suitable absorbers for UV light and are used in places where transparency and lack of influence of the additive on other desired properties are important [2].
Optical brighteners: Optical brighteners, which are also called fluorescent brightening agents, are used to reduce the yellowness of polymers, especially recycled polymers, which is caused by their use and aging. Some polymers such as PVC, PE, PU, PS, PMMA and copolymers require brightening agents.

The important thing that should be noted in these polishing compounds is that it must contain an aromatic ring or an aromatic heterocyclic ring. Also, double bands, without any distance from each other, should be conjugated in these compounds. Most of the brightening compounds are from the stilbene family or 4,4′-diaminostilbene, biphenyl, five-membered heterocycles (triazoles, oxazoles, imidazoles, etc.) or six-membered heterocyclic systems (coumarins, naphthalamides, triazines, etc.) [2].
Antioxidants: Antioxidants can stop or slow down the loss of mechanical properties caused by thermomechanical degradation during reprocessing steps. In other words, the presence of antioxidants can greatly improve the oxidation resistance of the polymer during the recycling process. Therefore, the role of antioxidants is to inhibit atmospheric oxidation during the process and consumption of the product. Antioxidants used in polymers are classified into primary and secondary categories. Primary antioxidants such as phenols and arylamines prevent the oxidation of polymers by eliminating free radicals (molecules separated from the polymer chain). Secondary antioxidants, including phosphite and sulfur compounds, stop the release of oxygenated radical molecules by breaking them down into stable products. German researchers studied the effect of antioxidants on the recycling of a waste polymer obtained from a separate batch of packaging. They found that the elastic modulus and tensile strength were slightly improved in the presence of antioxidant, while the elongation at break was significantly increased [2]. The figure below shows the structure of a phenolic antioxidant.

Moisture-absorbing masterbatches: due to the washing step in recycled polymer materials, there is a lot of moisture in these materials. Also, some polymer raw materials, fillers and pigments may have high humidity due to their polar nature.
The dehumidifier masterbatch is used as a drying and water absorbing agent to remove moisture from polymer and recycled raw materials such as polypropylene and polyethylene (LDPE, LLDPE, HDPE) in the process of film production by blowing or air, injection molding and air molding. The dehumidifier masterbatch can deal with the problems caused by moisture that are created during the production process of plastic products. The advantages of using dehumidifier masterbatch include reducing and eliminating fish eye and bubble defects, reducing of opacity and increasing of production speed, product strength increasing, extruder corrosion reducing and mechanical properties increasing.[1]
Restabilization
Restabilization is necessary to improve the quality of recycled materials. Stabilizers protect recycled materials from oxidative and photo-oxidative damage, thereby protecting the properties of the heat or light barrier both during the process and throughout the product’s life cycle. However, this is no different when raw materials are used. A minimum amount of stabilizer must be used during the original application to meet the application requirements of recycled materials. Also, any residual stabilizer from the initial use will aid in the recycling process. However, this usually is in itself not enough. All plastics that are primarily used in short-term applications such as the packaging industry rarely have stabilizers and no light protectors. In order to obtain a material that can meet the requirements, for example, for a long-term outdoor application, the recycled material must be restabilized.
The materials used in the restabilization of most recyclates (exception PVC), are mainly based on phenolic antioxidants, phosphites and costabilizers such as antacids for process and long-term thermal stabilization and hindered amine stabilizing (HAS) compounds and/or UV absorbers for light stabilization. Although the original stabilizer classes are not different from the raw materials, the appropriate stabilizer for recycled materials must consider the specific degradation characteristics of the recycled material. This means that the amount of stabilizer, the ratio between different types of stabilizers as well as the ratio between other additives should be optimized. As a rule, the optimized stabilizer with respect to price/performance will differ from the optimized stabilizer for the respective feedstock. Nevertheless, good primary stabilization of virgin materials is one of the prerequisites for high-quality recycling. It should be noted that restabilization before each recycling step is preferred, as opposed to over-stabilization in the first process.
Process stability, long-term thermal stability and mechanical properties are definitely improved by restabilization of recycled PP, for example higher values of impact strength (115 kJ/m2 vs. 62 kJ/m2 for unstabilized PP), strength tensile impact (430 kJ/m2 vs. 365 kJ/m2) and elongation (99% vs. 64%). Even recycled PP granules from municipal waste collection can compete with virgin materials in terms of process stability and thermal stability (OIT oxidation induction time) if the recycled is stabilized using RS-1 (a special recycled material stabilization system). Among the stabilizers, we can mention RS-1, RS-2, RS-3, RS-4. It should be mentioned that RS-3: a special combination that includes antioxidants, oxiranes, phosphites and costabilizers, RS-4: a special combination that includes antioxidants, phosphites, light stabilizers of hindered amines and costabilizers, and RS- 1, RS-2: a special combination includes antioxidants, phosphites and costabilizers.
Although recycling is environmentally beneficial and additives increase the quality of recycled products, the economic aspect must also be considered. The share of costs spent on additives, from small amounts (in the range of a few kilograms) to very large amounts, adds to the recycling costs[1].
Closed-loop recycling of filled polypropylene through restabilization
Fillers are generally used to reduce costs and change mechanical properties. For example, by adding fillers, the modulus is increased. But it has a negative effect on dimensional resistance and thermal resistance, tensile and flexural strength and elongation at break. Inorganic fillers such as calcium carbonate and talc have been found to significantly reduce the efficiency of light stabilizers (hindered amines, benzophenones) and antioxidants. In the presence of 0.05% of a common phenolic antioxidant (AO-2) at 120°C, polypropylene maintained 50% of its tensile strength for 3508 hours, but in the presence of 10% calcium carbonate, it was stable for only 470 hours and 10% talc for 2180 hours.
These negative effects in recycling should be considered. In a study on garden chairs filled with talc, the influence of restabilization on the processing, long-term heat aging and light stability were investigated. The item for recycling included garden chairs containing titanium dioxide and 15% calcium carbonate filler. Independent of the processing (double-screw or single-screw extruder), as shown in the table below, the non-restabilized materials showed a substantial increase of the melt flow resulting in some loss of mechanical properties.
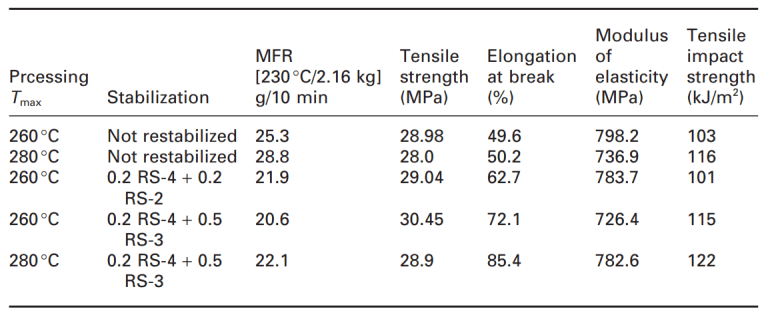
As expected, according to the table, degradation (increasing MFI) increases at higher process temperature. With restabilization, the melt flow can be kept at lower values independent of temperature, which indicates a reduction in the degradation of the composite during the process. In addition, restabilization including compounds containing reactive oxirane groups (RS-3) and acting as passivating fillers/coupling agents can improve mechanical properties such as elongation at break and tensile impact strength.
The stabilization and restability effect is also related to the long-term thermal properties of the filled recycled material, which has been tested up to 2000 hours at 135 degrees Celsius (Table 2). According to the table, the unstabilized material remains stable for only a few days, which is much shorter than what would be expected from unfilled polypropylene. During the obtained experiences, most mineral fillers, regardless of their structure, show a negative effect on the oxidative stability of the polymer. There is no doubt that mainly interactions between stabilizer and filler and adsorption/desorption mechanisms are responsible for this effect. Filler surface area and pore volume, surface functionality, hydrophilicity, thermal properties and light sensitivity of filler, the amount of transition metal ions (Mn, Fe, Ti) were considered as potential interaction parameters. Therefore, stabilizer formulations for filled plastics must include filler deactivators. The same is true for recycled materials containing fillers, such that reconsolidation with RS-3 increased the failure time and maintained the mechanical properties over time. With further increase in RS-3 concentration (1%), the values of tensile strength and tensile impact strength remained unchanged for 2000 hours at 135°C.

Since the garden chairs are an outdoor application, the weathering resistance of the filled recycled PP formulations was evaluated using a synthetic weathering test of up to 4000 hours (Table 3).

Unlike oven aging, where the loss of mechanical properties occurs very quickly and dramatically as soon as the stabilizers are consumed, the loss of mechanical properties during the artificial weathering test is slower because the degradation starts as a surface reaction and is exposed to specific exposures.; Until cracks appear and mechanical properties are destroyed. In any case, the unstabilized PP seat material lost about 60% of the initial tensile strength (which is currently lower than the stabilized formulation) before 1000 h of artificial weathering. Depending on the type of stabilizer and its concentration, even after 4000 hours, more than 90% of the initial tensile strength value was maintained. Therefore, what has been revealed is that the existence of a stabilization system containing filler inactivators (RS-3) in the recycled mixture has a great advantage [1].
References
[1] R. Pfaendner, Additives to upgrade mechanically recycled plastic composites, Management, Recycling and Reuse of Waste Composites, Elsevier2010, pp. 253-280.
[2] Q. Ding, H. Zhu, The key to solving plastic packaging wastes: Design for recycling and recycling technology, Polymers 15 (2023) 1485.
[3] M. Akbari, A. Zadhoush, M. Haghighat, PET/PP blending by using PP‐g‐MA synthesized by solid phase, Journal of applied polymer science 104 (2007) 3986-3993.
[4] D. Locatelli, A. Bernardi, L.R. Rubino, S. Gallo, A. Vitale, R. Bongiovanni, V. Barbera, M. Galimberti, Biosourced Janus Molecules as Silica Coupling Agents in Elastomer Composites for Tires with Lower Environmental Impact, ACS Sustainable Chemistry & Engineering 11 (2023) 2713-2726.
[5] https://www.raytopoba.com/Fluorescent-brightening-agent-OB-OB-1-FP-127-for-recycle-plastics_193.html.
[6]https://ariapolymer.ir/%d9%85%d8%ad%d8%b5%d9%88%d9%84%d8%a7%d8%aa/%d9%85%d8%b3%d8%aa%d8%b1%d8%a8%da%86-%d8%a7%d9%81%d8%b2%d9%88%d8%af%d9%86%db%8c/10062-2/.